Kehv veekindlus, ebatasane pind, suur pulbrisisaldus ja ebaühtlane pikkus?Levinud probleemid ja parendusmeetmed veesööda tootmisel
Igapäevasel veesööda tootmisel oleme kokku puutunud probleemidega erinevatest aspektidest.Siin on mõned näited, mida kõigiga arutada.
1, Valem
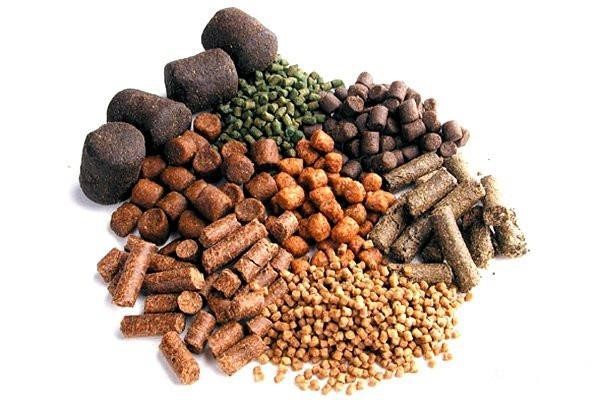
1. Kalasööda koostises on rohkem toorkiudude hulka kuuluvaid jahu tooraineid, nagu rapsiseemnejahu, puuvillajahu jne.Mõnel õlitehasel on arenenud tehnoloogia ja õli praetakse põhimõtteliselt kuivaks ja väga väikese sisaldusega.Pealegi ei ima seda tüüpi toorained tootmises kergesti, mis mõjutab granuleerimist palju.Lisaks on puuvillajahu raske purustada, mis mõjutab tõhusust.
2. Lahendus: suurendatud on rapsikoogi kasutamist ning segusse on lisatud kvaliteetseid kohalikke tooraineid nagu riisikliid.Lisaks on lisatud nisu, mis moodustab ligikaudu 5-8% segust.Läbi reguleerimise on 2009. aastal granuleerimisefekt suhteliselt ideaalne, samuti on tõusnud tonnisaak.2,5 mm osakesed on vahemikus 8-9 tonni, mis on varasemaga võrreldes ligi 2 tonni rohkem.Samuti on osakeste välimus oluliselt paranenud.
Lisaks segasime puuvillajahu purustamise efektiivsuse tõstmiseks enne purustamist puuvillajahu ja rapsiseemnejahu vahekorras 2:1.Pärast parandamist oli purustamiskiirus põhimõtteliselt võrdne rapsijahu purustamiskiirusega.
2, Osakeste ebaühtlane pind
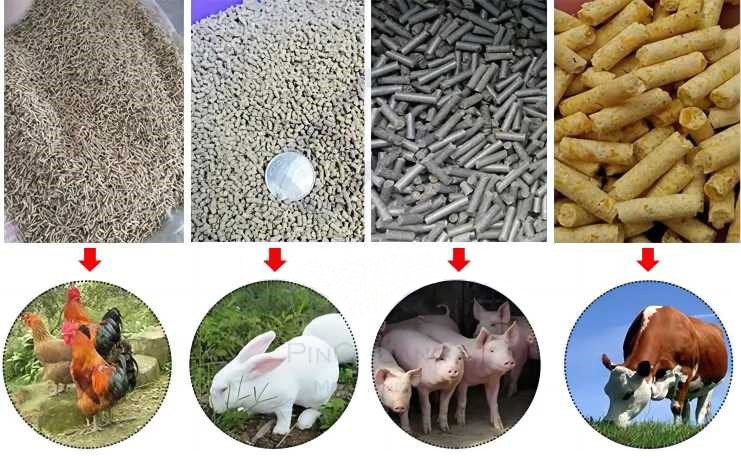
1. Sellel on suur mõju valmistoote välimusele ning vette lisatuna on see kalduvus lagunema ja selle kasutusmäär on madal.Peamine põhjus on:
(1) Toormaterjalid purustatakse liiga jämedalt ja karastamise ajal ei ole need täielikult laagerdunud ja pehmenenud ning neid ei saa vormiaukude läbimisel teiste toorainetega hästi kombineerida.
(2) Kõrge toorkiusisaldusega kalasööda segus purunevad need mullid, mis tulenevad karastamisprotsessi ajal tooraines leiduvatest aurumullidest, kuna osakeste kokkusurumisel tekib surve erinevus vormi sees ja väljaspool, mille tulemuseks on osakeste ebaühtlane pind.
2. Käitlemismeetmed:
(1) Kontrollige purustamisprotsessi korralikult
Praegu kasutab meie ettevõte kalasööda tootmisel lahtise toorainena 1,2 mm sõela mikropulbrit.Kontrollime sõela kasutussagedust ja haamri kulumisastet, et tagada purustamise peenus.
(2) Kontrollige aururõhku
Vastavalt valemile reguleerige aururõhku tootmise ajal mõistlikult, üldiselt kontrollides umbes 0,2.Kuna kalasööda koostises on palju jämedaid kiudaineid, on vaja kvaliteetset auru ja mõistlikku karastusaega.
3, Osakeste halb veekindlus
1. Seda tüüpi probleem on meie igapäevases tootmises kõige levinum, mis on üldiselt seotud järgmiste teguritega.
(1) Lühike karastamisaeg ja madal karastamistemperatuur põhjustavad ebaühtlase või ebapiisava karastamise, madala valmimisastme ja ebapiisava niiskuse.
(2) Ebapiisav liim, näiteks tärklis.
(3) Rõngasvormi surveaste on liiga madal.
(4) Õlisisaldus ja toorkiu tooraine osakaal valemis on liiga kõrge.
(5) Purustusosakeste suurusetegur.
2. Käitlemismeetmed:
(1) Parandage auru kvaliteeti, reguleerige regulaatori laba nurka, pikendage karastamisaega ja suurendage vastavalt tooraine niiskusesisaldust.
(2) Reguleerige valemit, suurendage sobivalt tärklise toorainet ning vähendage rasva ja toorkiu toorainete osakaalu.
(3) Vajadusel lisage liimi.(Naatriumipõhine bentoniidi suspensioon)
(4) Parandage surveastetring sureb
(5) Kontrollige hästi purustamise peenust
4, Liigne pulbri sisaldus osakestes
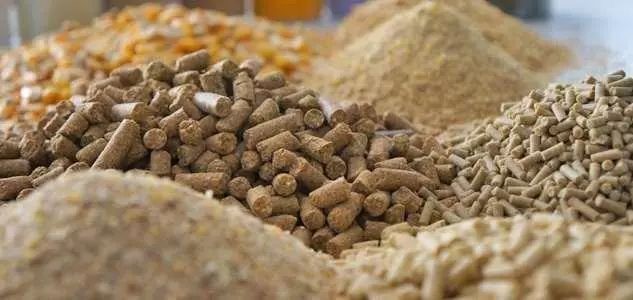
1. Pärast jahutamist ja enne sõelumist on raske tagada üldise pelletite sööda välimust.Kliendid on teatanud, et graanulites on rohkem peent tuhka ja pulbrit.Ülaltoodud analüüsi põhjal arvan, et sellel on mitu põhjust:
V. Osakeste pind ei ole sile, sisselõige ei ole korralik ja osakesed on lahtised ja kalduvad pulbri tootmisele;
B. mittetäielik sõelumine sorteerimissõelaga, ummistunud sõelavõrk, kummikuulide tugev kulumine, sõela sobimatu ava jne;
C. Valmistoote laos on palju peent tuha jääke ja tühjendamine ei ole põhjalik;
D. Tolmu eemaldamisel pakendamise ja kaalumise ajal on varjatud ohud;
Käsitsemismeetmed:
A. Optimeerige valemi struktuur, valige rõngasvorm mõistlikult ja kontrollige hästi tihendussuhet.
B. Toormaterjalide täielikuks küpsemiseks ja pehmendamiseks kontrollige granuleerimisprotsessi ajal karastamisaega, söötmiskogust ja granuleerimistemperatuuri.
C. Veenduge, et osakeste ristlõige oleks puhas ja kasutage terasribast valmistatud pehmet lõikenuga.
D. Reguleerige ja hooldage hindamisekraani ning kasutage mõistlikku ekraanikonfiguratsiooni.
E. Sekundaarse sõelumistehnoloogia kasutamine valmistoote lao all võib pulbrisisalduse suhet oluliselt vähendada.
F. Valmistoote ladu ja vooluringi on vaja õigeaegselt puhastada.Lisaks on vaja täiustada pakendit ja tolmueemaldusseadet.Tolmu eemaldamiseks on kõige parem kasutada negatiivset rõhku, mis on ideaalsem.Eriti pakkimisprotsessi ajal peaks pakendamistöötaja korrapäraselt koputama ja puhastama pakendikaalu puhverpunkrist tolmu..
5, Osakeste pikkus on erinev
1. Igapäevases tootmises puutume sageli kokku kontrolliga, eriti mudelite puhul, mille suurus on üle 420. Selle põhjused on kokkuvõtlikult järgmised:
(1) Granuleerimise söötmiskogus on ebaühtlane ja karastusefekt kõigub suuresti.
(2) Ebaühtlane vahe vormirullide vahel või rõngasvormi ja surverullide tugev kulumine.
(3) Rõngasvormi aksiaalsuunas on tühjenduskiirus mõlemas otsas madalam kui keskel.
(4) Rõngasvormi survet vähendav auk on liiga suur ja avanemiskiirus on liiga kõrge.
(5) Lõiketera asend ja nurk on ebamõistlikud.
(6) Granuleerimistemperatuur.
(7) Mõju avaldavad rõngasstantsi lõiketera tüüp ja tõhus kõrgus (tera laius, laius).
(8) Samal ajal on tooraine jaotus survekambris ebaühtlane.
2. Sööda ja graanulite kvaliteeti analüüsitakse üldiselt nende sisemiste ja väliste omaduste põhjal.Tootmissüsteemina puutume rohkem kokku söödagraanulite väliskvaliteediga seotud asjadega.Tootmise seisukohast võib veesöödagraanulite kvaliteeti mõjutavad tegurid kokku võtta järgmiselt:
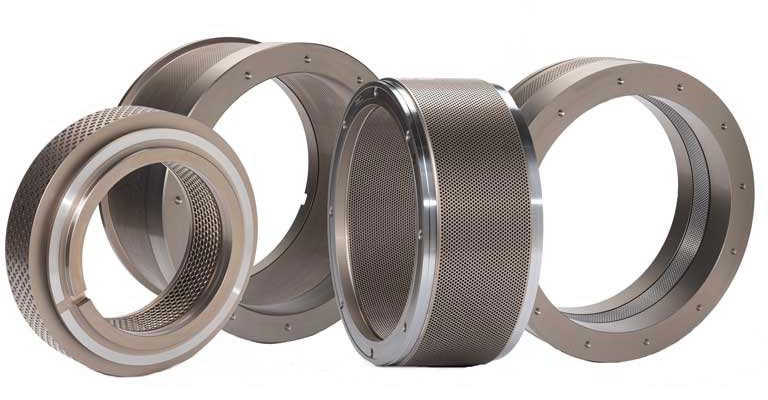
(1) Segude disain ja korraldus mõjutavad otseselt vees kasutatavate söödagraanulite kvaliteeti, moodustades ligikaudu 40% koguhulgast;
(2) purustamise intensiivsus ja osakeste suuruse ühtlus;
(3) Rõngasvormi läbimõõt, surveaste ja lineaarkiirus mõjutavad osakeste pikkust ja läbimõõtu;
(4) Rõngasvormi surveaste, lineaarkiirus, karastus- ja karastusefekt ning lõiketera mõju osakeste pikkusele;
(5) Valmistoodete niiskusesisaldust ja välimust mõjutavad tooraine niiskusesisaldus, karastusefekt, jahutamine ja kuivatamine;
(6) Seadmed ise, protsessitegurid ning karastus- ja karastusefektid mõjutavad osakeste pulbri sisaldust;
3. Käitlemismeetmed:
(1) Reguleerige kangakaabitsa pikkust, laiust ja nurka ning asendage kulunud kaabits.
(2) Pöörake tähelepanu lõiketera asendi õigeaegsele reguleerimisele tootmise alguses ja lõpus väikese etteandekoguse tõttu.
(3) Tootmisprotsessi ajal tagage stabiilne söötmiskiirus ja auruvarustus.Kui aururõhk on madal ja temperatuur ei saa tõusta, tuleks seda õigeaegselt reguleerida või peatada.
(4) Reguleerige mõistlikult vahetrulli kest.Järgige uut vormi uute rullidega ja parandage kiiresti surverulli ja rõngasvormi kulumise tõttu ebatasased pinnad.
(5) Parandage rõngasvormi juhtava ja puhastage koheselt ummistunud vormiauk.
(6) Rõngasvormi tellimisel võib algse rõngasvormi mõlemas otsas asuva kolme aukude rea surveaste olla 1-2 mm väiksem kui keskel.
(7) Kasutage pehmet lõikenuga, mille paksus on vahemikus 0,5–1 mm, et tagada võimalikult terav serv, nii et see oleks rõngasvormi ja surverulli vahelisel ühendusjoonel.
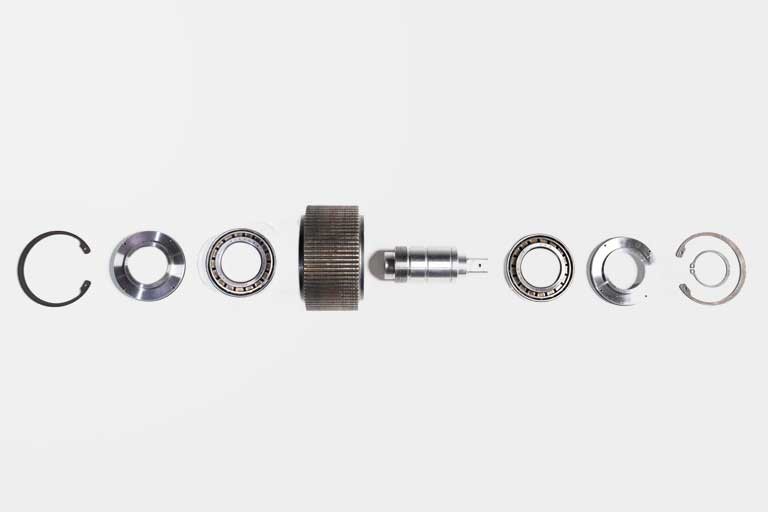
(8) Veenduge, et rõngasvormi kontsentrilisus, kontrollige regulaarselt granulaatori spindli kliirensit ja vajadusel reguleerige seda.
6, Kontrollpunktide kokkuvõte:
1. Lihvimine: jahvatamise peenust tuleb kontrollida vastavalt spetsifikatsiooni nõuetele
2. Segamine: Tooraine segamise ühtlust tuleb kontrollida, et tagada sobiv segamiskogus, segamisaeg, niiskusesisaldus ja temperatuur.
3. Laagerdumine: paisutamismasina rõhku, temperatuuri ja niiskust tuleb kontrollida
Osakeste materjali suurus ja kuju: tuleb valida sobivad survevormide ja lõiketerade spetsifikatsioonid.
5. Valmissööda veesisaldus: On vaja tagada kuivamis- ja jahutusaeg ning temperatuur.
6. Õli pihustamine: On vaja kontrollida täpset pihustatud õli kogust, düüside arvu ja õli kvaliteeti.
7. Sõelumine: valige sõela suurus vastavalt materjali spetsifikatsioonidele.
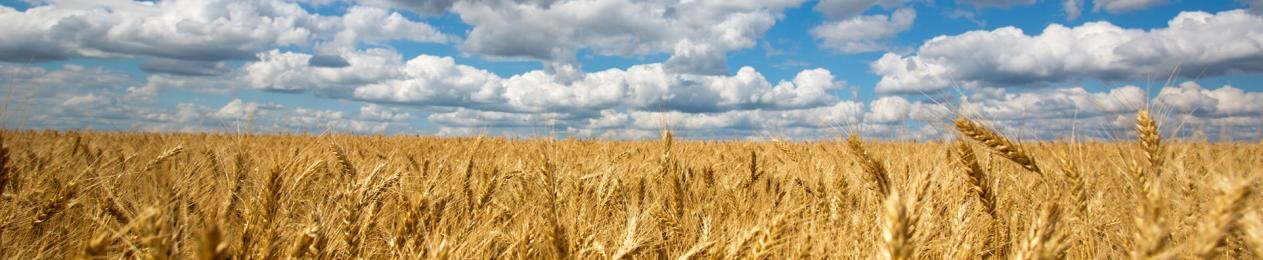
Postitusaeg: 30. november 2023