Kehv veekindlus, ebaühtlane pind, suur pulbrisisaldus ja ebaühtlane pikkus? Levinud probleemid ja parendusmeetmed veelookste tootmisel
Meie igapäevases veelootmise tootmises oleme kokku puutunud mitmesuguste probleemidega. Siin on mõned näited, mida kõigiga arutada:
1, Valem
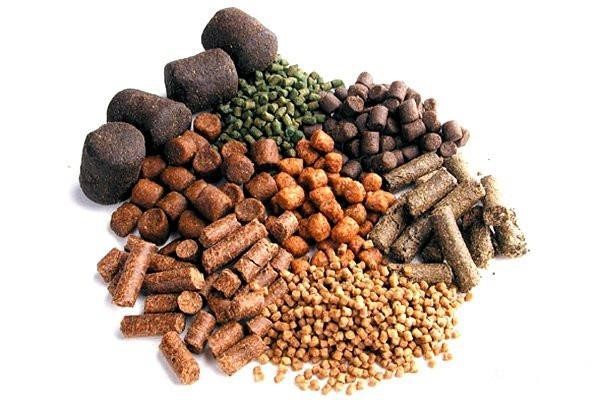
1. Kalasööda valemistruktuuris on mitut tüüpi jahu tooraineid, näiteks rapsiseemnejahu, puuvillajahu jne, mis kuuluvad toorkiu hulka. Mõnel õlitehasel on täiustatud tehnoloogia ja õli praaditakse põhimõtteliselt kuivaks, väga vähese sisaldusega. Lisaks ei imendu seda tüüpi toorained tootmises kergesti, mis mõjutab oluliselt granulatsiooni. Lisaks on puuvillajahu raske purustada, mis mõjutab efektiivsust.
2. Lahendus: Rapsikoogi kasutamist on suurendatud ja valemisse on lisatud kvaliteetseid kohalikke koostisosi, näiteks riisikliisid. Lisaks on lisatud nisu, mis moodustab valemist umbes 5–8%. Kohandamise abil on granulatsiooniefekt 2009. aastal suhteliselt ideaalne ja ka saagikus tonni kohta on suurenenud. 2,5 mm osakesed on 8–9 tonni vahel, mis on ligi 2 tonni rohkem kui varem. Ka osakeste välimus on oluliselt paranenud.
Lisaks segasime puuvillaseemnejahu purustamise efektiivsuse parandamiseks enne purustamist puuvillaseemnejahu ja rapsiseemnejahu vahekorras 2:1. Pärast täiustamist oli purustuskiirus põhimõtteliselt võrdne rapsiseemnejahu purustuskiirusega.
2, Osakeste ebaühtlane pind
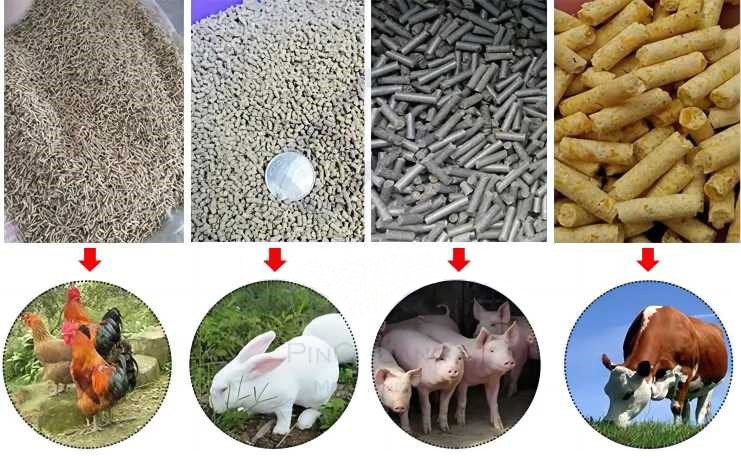
1. Sellel on suur mõju valmistoote välimusele ning vette lisamisel on see altid kokku varisema ja selle kasutusmäär on madal. Peamine põhjus on:
(1) Toorained purustatakse liiga jämedalt ning karastamise käigus ei ole need täielikult küpsenud ja pehmenenud ning neid ei saa vormi aukudest läbi minnes teiste toorainetega hästi kombineerida.
(2) Suure toorkiu sisaldusega kalasööda valemis tekivad karastamise ajal tooraines aurumullid, mis purunevad osakeste kokkusurumise ajal vormi sise- ja välispinna vahelise rõhuerinevuse tõttu, mille tulemuseks on osakeste ebaühtlane pind.
2. Käitlemismeetmed:
(1) Kontrollige purustusprotsessi korralikult
Praegu kasutab meie ettevõte kalasööda tootmisel puistematerjalina 1,2 mm sõelaga mikropulbrit. Purustamise peenuse tagamiseks kontrollime sõela kasutussagedust ja haamri kulumisastet.
(2) Auru rõhu reguleerimine
Valemi kohaselt reguleerige aururõhku tootmise ajal mõistlikult, kontrollides üldiselt umbes 0,2. Kalasööda valemis sisalduva suure hulga jämedate kiudainete tõttu on vaja kvaliteetset auru ja mõistlikku karastamisaega.
3, Osakeste halb veekindlus
1. Seda tüüpi probleem on meie igapäevases tootmises kõige levinum ja on üldiselt seotud järgmiste teguritega:
(1) Lühike karastusaeg ja madal karastustemperatuur põhjustavad ebaühtlast või ebapiisavat karastamist, madalat valmimisastet ja ebapiisavat niiskust.
(2) Ebapiisav liimmaterjalide, näiteks tärklise, hulk.
(3) Rõngasvormi surveaste on liiga madal.
(4) Valemi õlisisaldus ja toorkiudainete osakaal on liiga kõrge.
(5) Purustavate osakeste suurustegur.
2. Käitlemismeetmed:
(1) Parandage auru kvaliteeti, reguleerige regulaatori laba nurka, pikendage karastamisaega ja suurendage vastavalt tooraine niiskusesisaldust.
(2) Reguleerige valemit, suurendage vastavalt tärklise tooraine sisaldust ning vähendage rasva ja toorkiudainete osakaalu.
(3) Vajadusel lisage liimi. (Naatriumipõhine bentoniidi suspensioon)
(4) Parandage tihendussuhetrõngasstants
(5) Kontrollige purustamise peenust hästi
4, Liigne pulbrisisaldus osakestes
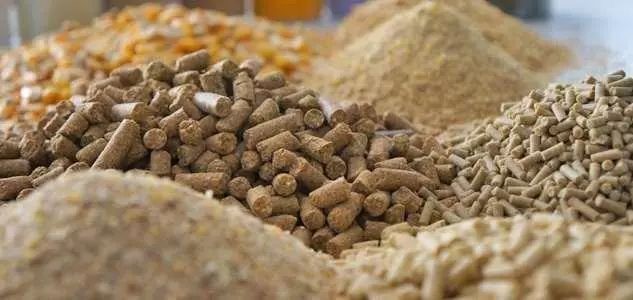
1. Pärast jahutamist ja enne sõelumist on üldise graanulite sööda välimust raske tagada. Kliendid on teatanud, et graanulites on rohkem peent tuhka ja pulbrit. Eeltoodud analüüsi põhjal arvan, et sellel on mitu põhjust:
A. Osakeste pind ei ole sile, sisselõige ei ole puhas ning osakesed on lahtised ja altid pulbri tootmisele;
B. Puudulik sõelumine sorteerimissõela abil, ummistunud sõelavõrk, kummipallide tugev kulumine, sobimatu sõelavõrgu ava jne;
C. Valmistoodangu laos on palju peent tuhajääki ja kliirens ei ole põhjalik;
D. Pakendamise ja kaalumise ajal tolmu eemaldamisel on varjatud ohud;
Käitlemismeetmed:
A. Optimeerige valemi struktuuri, valige rõngasvorm mõistlikult ja kontrollige surveastet hästi.
B. Granuleerimisprotsessi ajal kontrollige karastamisaega, söötmiskogust ja granuleerimistemperatuuri, et toorained täielikult valmiksid ja pehmeneksid.
C. Veenduge, et osakeste ristlõige oleks puhas ja kasutage pehmet terasribast lõikenuga.
D. Kohanda ja hoolda hindamisekraani ning kasuta mõistlikku ekraanikonfiguratsiooni.
E. Valmistoote laos sekundaarse sõelumistehnoloogia kasutamine võib pulbri sisalduse suhet oluliselt vähendada.
F. Valmistoodangu ladu ja ringlust on vaja õigeaegselt puhastada. Lisaks on vaja täiustada pakendit ja tolmu eemaldamise seadet. Tolmu eemaldamiseks on kõige parem kasutada negatiivset rõhku, mis on ideaalsem. Eriti pakendamisprotsessi ajal peaks pakendaja regulaarselt pakendikaalu puhverpunkrit tolmust puhastama..
5, Osakeste pikkus varieerub
1. Igapäevases tootmises kohtame sageli raskusi juhtimisega, eriti mudelite puhul, mis on suuremad kui 420. Selle põhjused on kokku võetud järgmiselt:
(1) Granuleerimise söötmiskogus on ebaühtlane ja karastamisefekt kõigub suuresti.
(2) Vormirullide vaheline ebaühtlane vahe või rõngasvormi ja surverullide tugev kulumine.
(3) Rõngasvormi aksiaalsuunas on tühjenduskiirus mõlemas otsas madalam kui keskel.
(4) Rõngasvormi rõhu alandamise auk on liiga suur ja avamiskiirus on liiga kõrge.
(5) Lõiketera asend ja nurk on ebamõistlikud.
(6) Granuleerimistemperatuur.
(7) Rõngaslõiketera tüüp ja efektiivne kõrgus (tera laius, laius) mõjutavad tulemust.
(8) Samal ajal on tooraine jaotus survekambris ebaühtlane.
2. Sööda ja graanulite kvaliteeti analüüsitakse üldiselt nende sisemiste ja väliste omaduste põhjal. Tootmissüsteemina oleme rohkem kokku puutunud söödagraanulite välise kvaliteediga seotud asjadega. Tootmise seisukohast saab veelisööda graanulite kvaliteeti mõjutavad tegurid kokku võtta järgmiselt:
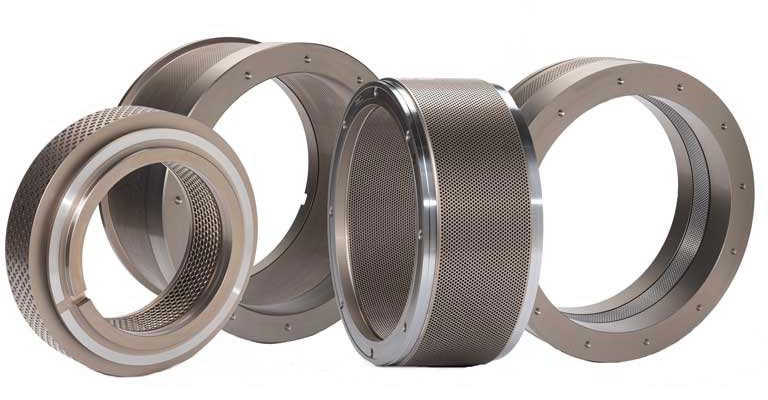
(1) Piimasegude ülesehitus ja korraldus mõjutavad otseselt veelisööda graanulite kvaliteeti, moodustades ligikaudu 40% koguhulgast;
(2) purustamise intensiivsus ja osakeste suuruse ühtlus;
(3) Rõngasvormi läbimõõt, surveaste ja lineaarkiirus mõjutavad osakeste pikkust ja läbimõõtu;
(4) rõngasvormi surveaste, lineaarkiirus, karastus- ja noolutusmõju ning lõiketera mõju osakeste pikkusele;
(5) Toormaterjalide niiskusesisaldus, karastamine, jahutamine ja kuivatamine mõjutavad valmistoodete niiskusesisaldust ja välimust;
(6) Seadmed ise, protsessitegurid ning karastus- ja noolustusefektid mõjutavad osakeste pulbri sisaldust;
3. Käitlemismeetmed:
(1) Reguleerige kangakaabitsa pikkust, laiust ja nurka ning vahetage kulunud kaabits välja.
(2) Pöörake tähelepanu lõiketera asendi õigeaegsele reguleerimisele tootmise alguses ja lõpus väikese etteandekoguse tõttu.
(3) Tootmisprotsessi ajal tuleb tagada stabiilne etteandekiirus ja auruvarustus. Kui aururõhk on madal ja temperatuur ei saa tõusta, tuleks seda õigeaegselt reguleerida või peatada.
(4) Reguleerige mõistlikult vahetrullkestUue vormi järel paigaldage uued rullid ja parandage koheselt surverulli ja rõngasvormi kulumisest tingitud ebatasased pinnad.
(5) Parandage rõngasvormi juhtava ja puhastage ummistunud vormiava viivitamatult.
(6) Rõngasvormi tellimisel võib algse rõngasvormi aksiaalsuuna mõlemas otsas olevate kolme aukude rea surveaste olla 1–2 mm väiksem kui keskel.
(7) Kasutage pehmet lõikenuga, mille paksus on 0,5–1 mm, et tagada võimalikult terav serv, nii et see jääks rõngasvormi ja surverulli vahelisele ühendusjoonele.
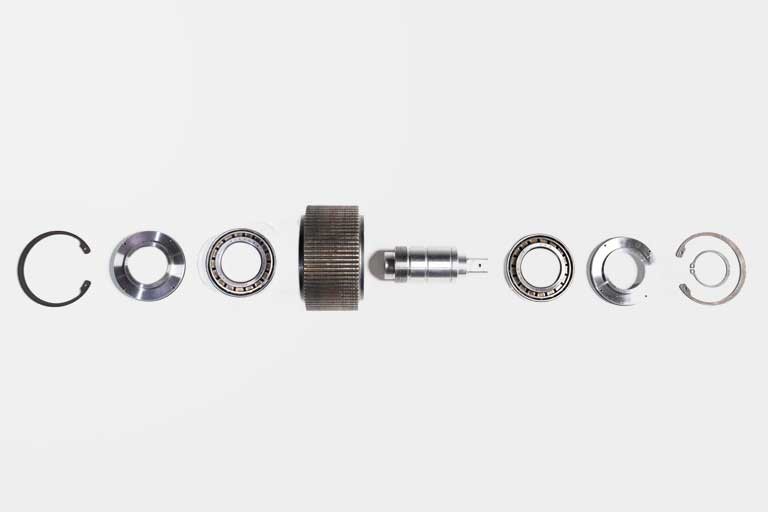
(8) Veenduge rõngasvormi kontsentrilisuses, kontrollige regulaarselt granulaatori spindli kliirensit ja vajadusel reguleerige seda.
6, Kokkuvõtlikud kontrollpunktid:
1. Jahvatamine: Jahvatamise peenust tuleb kontrollida vastavalt spetsifikatsiooninõuetele
2. Segamine: Tooraine segamise ühtlust tuleb kontrollida, et tagada sobiv segamiskogus, segamisaeg, niiskusesisaldus ja temperatuur.
3. Küpsemine: Paisutusmasina rõhku, temperatuuri ja niiskust tuleb kontrollida
Osakeste materjali suurus ja kuju: tuleb valida sobivad survevormide ja lõiketerade spetsifikatsioonid.
5. Valmis sööda veesisaldus: on vaja tagada kuivamis- ja jahutusaeg ning -temperatuur.
6. Õli pihustamine: On vaja kontrollida õli pihustamise täpset kogust, düüside arvu ja õli kvaliteeti.
7. Sõelumine: Valige sõela suurus vastavalt materjali spetsifikatsioonidele.
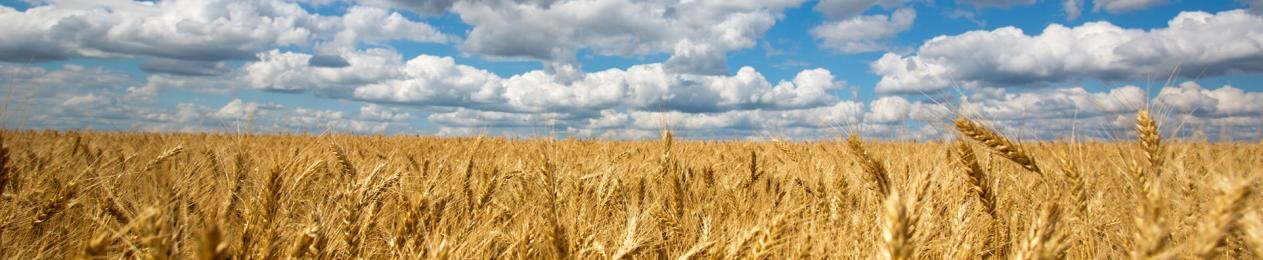
Postituse aeg: 30. november 2023